MANUFACTURING PROCESS ENGINEERING
160+ Years of Improvement, Quality, and PerformanceEXPERTISE TO HELP GET THE JOB DONE
Our experts are seasoned manufacturing industry professionals experienced in complex systems. With precision shredding and material movement at the heart of what we do, we can optimize and automate your manual process. We can improve your existing processes, or we can create a new process by collaborating during the R&D stages. We work hard to development our relationships with our equipment suppliers so that your experience with us, and them, is completely seamless.
SPECIALIZED KNOWLEDGE
![]() |
TISSUE MANUFACTURING |
![]() |
CORRUGATED CARDBOARD |
![]() |
MANUFACTURING PROCESSES THAT USE FOAM |
![]() |
INDUSTRIAL SHREDDING |
THE ENGINEERING PROCESS
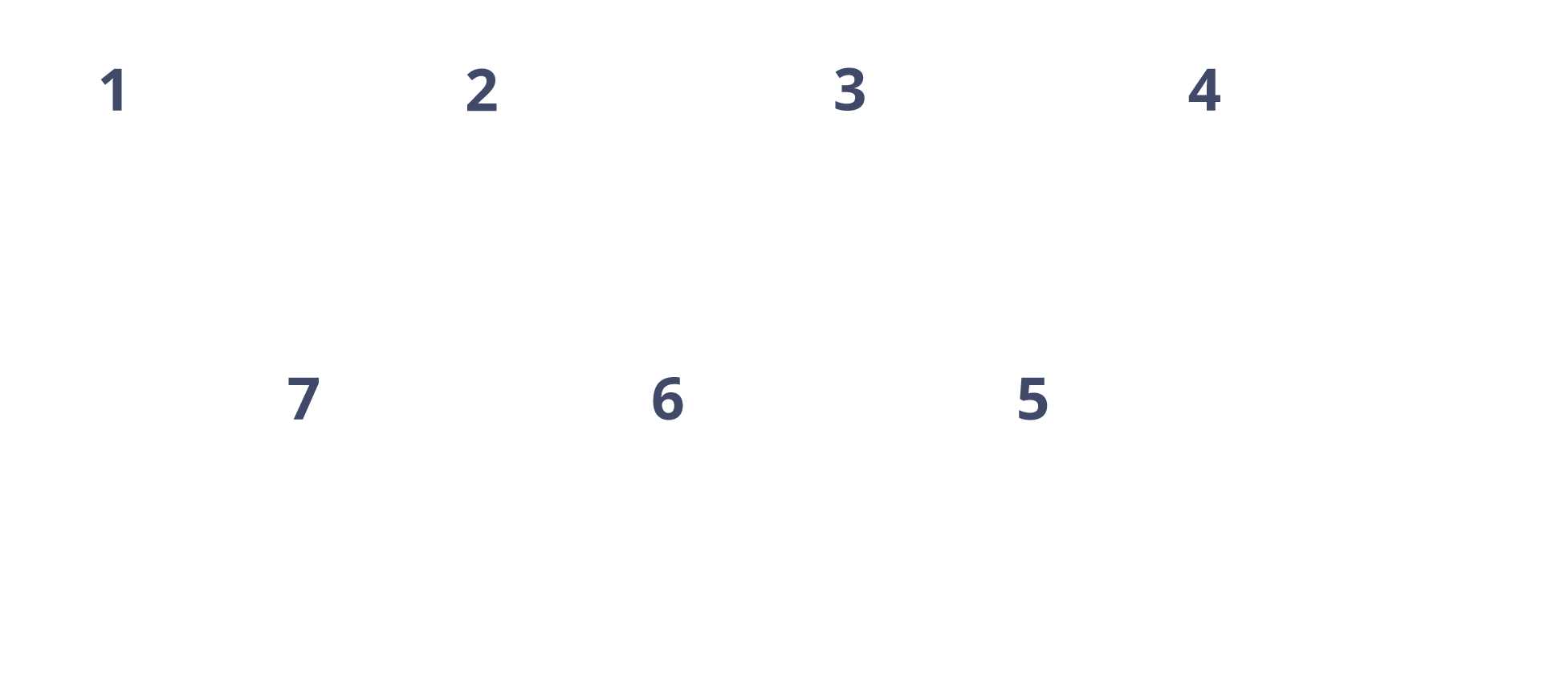
1. EVALUATE APPLICATION
Go through an investigative process to evaluate pre- and post-shredded product, volume, system parameters, process parameters, material parameters.
2. DESIGN SYSTEM
Provide a layout of all of the equipment in the system as well as specifications for each piece of equipment.
3. PROPOSE SOLUTION
Present an informal solution with proposed equipment -- demonstrate expertise and ability to solve the challenge.
4. COORDINATE SCHEDULES
Manage manufacturing of equipment, including coordinating lead times, shipping, and installation dates.
5. OVERSEE INSTALLATION
Ensure that all relevant equipment and labor arrive on the site within the specified time frame.
6. LAUNCH AND OPTIMIZE SYSTEMS
Provide a single point of contact to customer to ensure that the system is installed correctly and with the expected quality and timeframe.
7. POST-INSTALLATION SUPPORT
SCHEDULE TIME TO TALK
Speak with our solutions expert to talk through your needs.